Comprehending the Fundamentals and Applications of Plastic Extrusion in Modern Manufacturing
In the realm of modern-day production, the strategy of plastic extrusion plays an instrumental function - plastic extrusion. This intricate procedure, involving the melting and shaping of plastic via specialized passes away, is leveraged throughout numerous sectors for the development of varied items. From auto components to customer goods packaging, the applications are huge, and the possibility for sustainability is similarly excellent. Unwinding the principles of this process discloses real flexibility and potential of plastic extrusion.
The Principles of Plastic Extrusion Process
While it may appear complicated, the principles of the plastic extrusion procedure are based on reasonably simple principles. It is a manufacturing process wherein plastic is thawed and then formed into a continuous profile with a die. The plastic extrusion procedure is extensively made use of in various sectors due to its performance, versatility, and cost-effectiveness.
Different Kinds of Plastic Extrusion Methods
Structure upon the basic understanding of the plastic extrusion process, it is needed to explore the various techniques entailed in this manufacturing method. In comparison, sheet extrusion develops big, level sheets of plastic, which are commonly additional processed into products such as food packaging, shower drapes, and cars and truck parts. Recognizing these methods is vital to using plastic extrusion effectively in modern production.
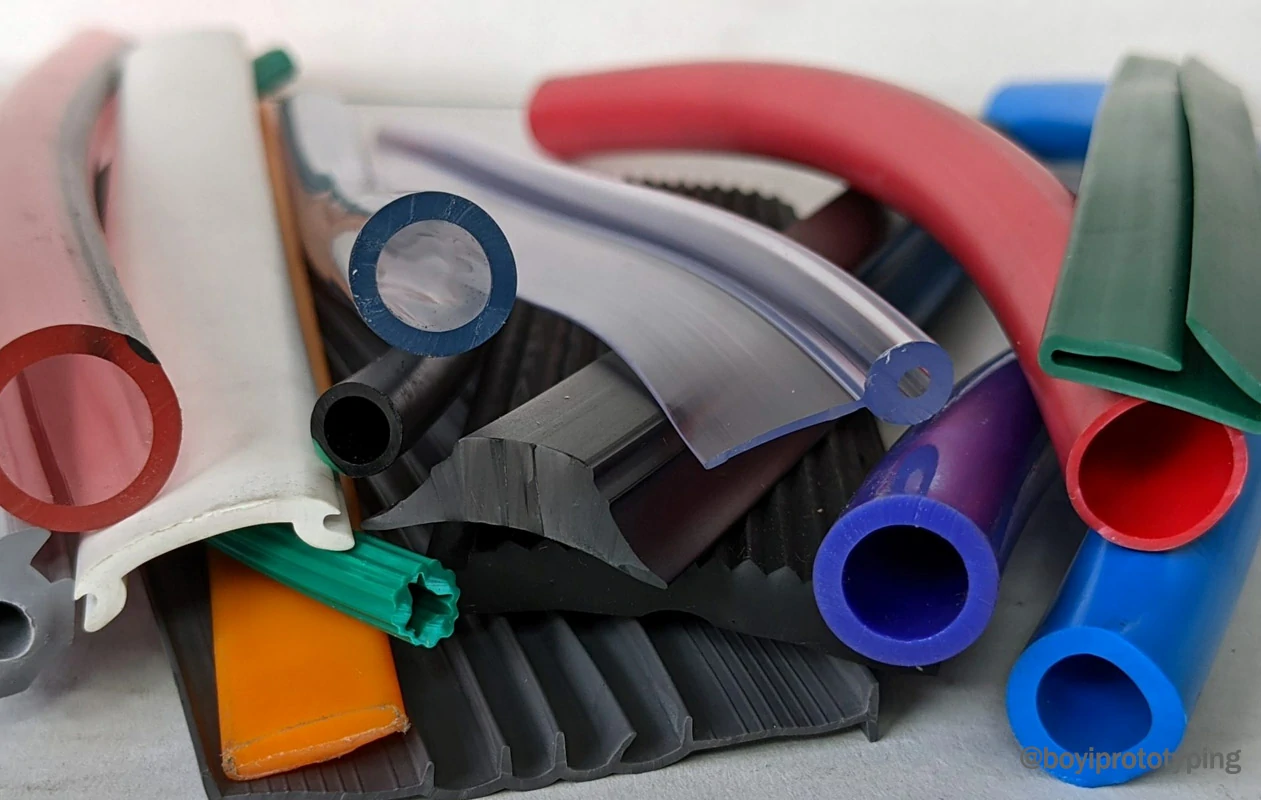
The Function of Plastic Extrusion in the Automotive Market
A frustrating bulk of components in contemporary cars are items of the plastic extrusion process. This procedure has actually revolutionized the vehicle market, transforming it into a much more efficient, cost-efficient, and versatile production market. Plastic extrusion is primarily made use of in the manufacturing of numerous automobile components such as bumpers, grills, door panels, and dashboard trim. The procedure supplies an attire, regular output, enabling suppliers to create high-volume components with great accuracy and marginal waste. The lightness of the extruded plastic components adds to the total reduction in vehicle weight, enhancing fuel efficiency. Furthermore, the toughness and resistance of these parts to heat, chilly, and influence enhance the long life of automobiles. Thus, plastic extrusion plays an essential duty in auto manufacturing.
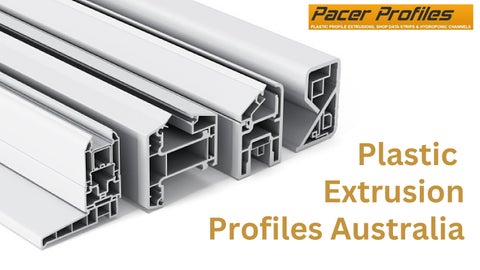
Applications of Plastic Extrusion in Consumer Goods Manufacturing
Past its substantial effect on the automotive sector, plastic extrusion verifies just as reliable in the realm of consumer goods manufacturing. This procedure is critical in developing a wide variety of items, from food product packaging to household home appliances, toys, and even clinical devices. The convenience of plastic extrusion allows manufacturers to design and generate intricate shapes and sizes with high accuracy and effectiveness. Furthermore, due to the recyclability of several plastics, extruded go to my site parts can be recycled, decreasing waste and expense. The versatility, adaptability, and cost-effectiveness of plastic extrusion make it a favored choice for several customer products producers, adding dramatically to the market's growth and advancement. The environmental effects of this try these out prevalent usage call for cautious factor to consider, a topic to be reviewed additionally in the subsequent section.
Ecological Influence and Sustainability in Plastic Extrusion
The prevalent use of plastic extrusion in producing welcomes scrutiny of its ecological ramifications. Effective machinery reduces energy use, while waste management systems reuse scrap plastic, lowering raw product needs. Despite these enhancements, even more development is needed to reduce the ecological footprint of plastic extrusion.
Final thought
In verdict, plastic extrusion plays a critical duty in contemporary manufacturing, specifically in the auto and consumer goods sectors. Its adaptability enables the manufacturing of a large range of components with high accuracy. In addition, its capacity for recycling and growth of naturally degradable materials offers a promising opportunity towards lasting techniques, thereby addressing ecological concerns. Recognizing the fundamentals of this procedure is essential to enhancing its applications and benefits.
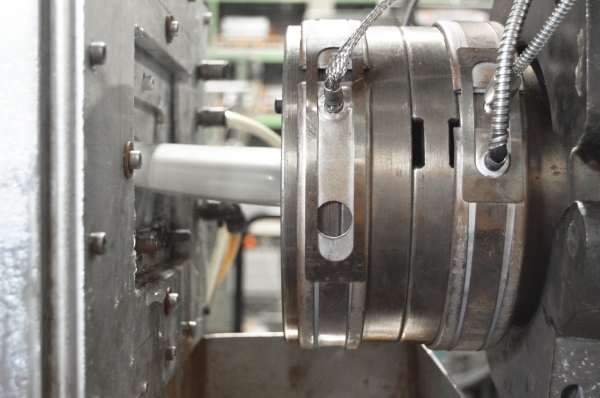
The plastic i loved this extrusion process is thoroughly made use of in various sectors due to its adaptability, cost-effectiveness, and performance.
Structure upon the basic understanding of the plastic extrusion procedure, it is needed to discover the numerous techniques involved in this manufacturing method. plastic extrusion. In comparison, sheet extrusion develops big, flat sheets of plastic, which are usually more refined into products such as food packaging, shower curtains, and car components.An overwhelming bulk of components in modern lorries are products of the plastic extrusion procedure
Comments on “Plastic extrusion for durable and lightweight components”